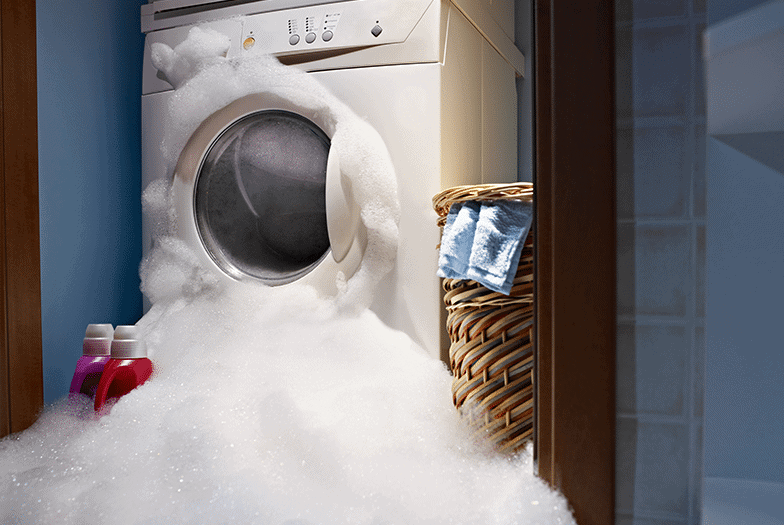
Cheap Product or Misuse?
Did you buy a lemon or is the way you’re using your appliance causing it to break prematurely?
In the world of mechanical and electronic devices, there are written and unwritten rules on how to operate them to get the maximum life span out of it. Traditionally, there are user manuals that spell out how the manufacturer expects the product to be operated to reduce unexpected failures. With that being said, most people don’t spend the time to read the manual and use their past experiences to guide them with their new product. The amount of times I’ve heard, “I’ve had a refrigerator my entire life, I know how to use one.” or “I’ve been using a washer since I was little, there’s not much you can teach me.” Is enough to make me rip my hair out. To make things worse, these same people throw around the phrases, “I got a lemon!” or “my old one didn’t do this!” when something breaks. Unfortunately, most warranty service calls are caused by the client not using it correctly or doing something that causes the machine to break. In our experience, up to 50% of warranty jobs are caused by something other than the machine breaking or what we call, customer instruct calls. In the manufacturer’s eyes, customer instruct calls are non-warrantable and we as servicers are either on the hook for the service, or we need to charge the customer. Being a servicer of empathy, we unfortunately can’t charge a customer for something that is still under the warranty period. Instead, we try to educate them so it doesn’t happen again, usually to no avail.
With such a large amount of service calls not really involving a broken part that needs to be replaced, what is the deal? Why does it seem that products are becoming usable for only a few years before you need to buy a new one? Although there are several answers to this, most of them can be summed up by the fact that most people become unhappy with a product after a single failure, whether it was the machine or misuse. Ask yourself this. Have you ever had a failure in a car, had it repaired and the first time you drove it you think there a different noise or something else wrong with it? This is due to you being hyper aware of your car now that it has had a failure. The odds are, that “new” sound was there before you took your car in, but you didn’t pay attention to it because it was actually a normal sound of operation. The issue is, now that you’ve had one problem, you think there is another one. Then when something else goes wrong, you start to incorrectly tally these failures and before you know it you think your vehicle has broken down 5 times. This happens with appliances as well. Let’s say you bought a new front load washer because you wanted to try something different than your old top loader. In the first few uses, you realize there are a bunch of soap suds, there’s a code displaying and it won’t unlock the door. A tech comes out, clears out the soap suds, checks the machine out and everything is working correctly, you just used too much soap. Unfortunately, most of the time people go to the old tried and true statement, “my old one didn’t do that.” Then when you ask if they checked out the manual, you get my other favorite statement, “I’ve been washing longer than you’ve been alive. I don’t need a manual.” This experience is going to negatively affect how the consumer views their appliance for the rest of its lifespan, and in some cases, cause it to be replaced long before it really needed to be. In the consumer’s eyes, the product should operate as they intend, in the techs eyes, the product is doing exactly what it should be doing, it’s just being misused.
With that being said, we are living in a time where things are being made cheaper with the invention of more sophisticated manufacturing equipment. There are more electronic control boards, more plastic and that does cause things to breakdown faster if you are unaware of how to handle it. With manufacturing practices becoming more streamlined, more manufacturers and brands that haven’t made major appliance in the past, are starting to make major appliances. Manufacturers that once made only electronic devices are now starting to venture into the world of mechanical devices. Brands that have been around for 50 or even 100 years have been in constant research and development to make sure the parts that are going into their product can last the test of time. With newer brands, sometimes they will develop a product and a few years later, a part will fail because of a manufacturing flaw. In most cases, they will either send you the exact same part that has already failed, or go in a completely different direction; reinventing the wheel if you will. This is an issue because there is constantly a new product being made, instead of making the old one better. For instance, instead of having the Ford F-150 model lasting since 1974, we would be on the latest ideation, the Ford F-2450. This constant redesigning makes it to where a good idea that has minor flaws, is scrapped in order to make something new, usually with more innovative features, which doesn’t necessarily make it last longer. In years past, manufacturers like Maytag and Whirlpool would have the same design washer and dryer for 20 or even 40 years, with varying features like a quiet package or more buttons. Now a days, you’d be happy to find a design that has been around 10 years.
Through my years of being an appliance technician, I’ve learned a lot about people and how they use their products. Most people mean well with their intentions; reading manuals, researching online about tips and tricks and overall trying to handle their investment with as much care as possible. However, sometimes what we are reading isn’t as solid as we wish it would be. Sometimes we read or watch advertisements and expect what they are saying to be held as factual and 100% true. The harsh reality is that these advertisements are designed to sell a product. When you hear that fabric softner is something you should be using in your washing machine, you believe that to be true. Unfortunately, add on products aren’t something you need in your washer and something that can actually harm your machine. Softner is something that when overused, can create a mold issue that will eventually make your machine smell foul. The first time you get a whiff of it, you start to look for a product to remove it. Enter the new pellets you can add to your wash to help your clothes and washer smell good after use. It’s like we’re constantly on the search for a new product to use. The issue from a tech standpoint is that you shouldn’t have to mask the smell of your washer. Correct care from the 1st day you received your washer should be top priority. Trust in the manufacturer or your dealer to ensure they will give you correct info. When a delivery or service tech says you should be using very little soap, take that advice. We are aware the manufacturer says to use an entire cup of soap or 3 pods for large loads, but it is not something you want to do if you want a good smelling, long lasting machine. The soap manufacturers are looking to sell soap, of course they are going to tell you to use 3x more than you really need. In reality, energy efficient or HE washers could get away with a few table spoons of soap and still get your clothes just as clean.
We as technicians are here to help you maintain your home appliances so you can continue to use them for a long time. Sometimes, we come off as know it all's when we say one thing or another. We know that there are certain flaws with certain machines and we try to guide you in a way that helps you operate the machine in a manner that will keep you from having to deal with these flaws. For the most part, if a product is used gently and within the manufacturer’s guidelines, you’re in for many years of trouble free usage. If something does happen and a tech gives you a piece of advice, listen up, ask questions. You may learn something that you can pass on to a friend or loved one because we all deal with the same issues, just at different times.
If you enjoy this content, consider leaving a comment with a question or topic for our next article. You may find it discussed in our next article.